LB2000 FOR CNC MACHINING
LB2000 micro-lubricant is usually used in metal processing, such as precision turning, milling, drilling, tapping and other processing techniques. It can provide good lubrication and cooling between the tool and the workpiece, and is especially suitable for occasions with high processing accuracy requirements, such as aerospace parts processing, precision electronic equipment parts manufacturing, etc.
Preparation before use
Equipment inspection
Ensure that the lubrication system of processing equipment (such as machine tools) using trace lubricants is clean and free of impurities. Check whether the nozzle or oil injection device is blocked. If blocked, clean or replace it.
Verify that the pressure regulation system, flow control system and other functions of the equipment are normal and can accurately deliver lubricants to the processing area.
Lubricant inspection
Observe the appearance of LB2000 trace lubricant. There should be no obvious stratification, precipitation or discoloration. If there is any abnormality, it may mean that the lubricant has deteriorated and should not be used.
Check the packaging label of the lubricant to confirm that its specifications and models meet the requirements of the equipment and processing technology.
How to use
Refueling
According to the equipment’s tank capacity and actual processing requirements, add an appropriate amount of LB2000 micro-lubricant to the equipment’s tank. During the refueling process, it is best to use a funnel with a filter to prevent impurities from entering the tank. Generally speaking, when refueling for the first time, do not exceed 80% of the tank capacity to avoid lubricant overflow during equipment operation.
System Settings
Turn on the equipment’s lubrication system and adjust the pressure and flow of the lubricant. For micro-lubricants, the flow is usually set to a lower level to achieve precise micro-lubrication. The pressure is generally determined by the type of nozzle and the processing requirements, usually between 1 – 5 bar. For example, in some small precision drilling processes, the pressure can be set to about 2 bar, and the flow rate is controlled within the range of a few drops to more than ten drops per minute.
Set the frequency and time of oil injection. It can be adjusted according to factors such as the rotation speed of the machining tool, the feed speed, and the material of the workpiece being processed. For example, when milling aluminum alloy workpieces at high speed, the oil injection frequency can be relatively high, with oil injection once for every turn of the tool or every feed of a certain distance (such as every 5 – 10mm).
Monitoring during machining
During machining, the use of lubricating oil should be continuously observed. Check whether the nozzle sprays oil normally and whether the lubricating oil can be accurately sprayed to the contact area between the tool and the workpiece. If uneven oil spraying or blockage is found, the machining should be stopped immediately and the lubrication system should be inspected and repaired.
Pay attention to the machining quality, such as the roughness of the machining surface and the wear of the tool. If the quality of the machining surface is found to be reduced or the tool wears too quickly, it may be necessary to adjust the parameters of the lubricating oil appropriately, such as increasing the flow rate or changing the injection angle.
Safety precautions
Avoid contact with skin and eyes
LB2000 micro-lubricant may cause irritation to skin and eyes. During operation, if the lubricant accidentally contacts the skin, rinse immediately with plenty of water. If it contacts the eyes, rinse quickly with water for at least 15 minutes and seek medical attention in time.
Good ventilation
The use place should maintain a good ventilation environment to reduce the oil and gas concentration generated by the volatilization of the lubricant. Prolonged exposure to a high concentration of oil and gas may cause harm to human health.
Storage conditions
Temperature
LB2000 micro-lubricant should be stored indoors, away from direct sunlight, and preferably at an ambient temperature between 5 and 40 degrees Celsius. Too high a temperature may cause the lubricant to deteriorate, while too low a temperature may affect its fluidity.
Seal
Lubricant containers should be well sealed to prevent dust, moisture and other impurities from entering. Unused lubricants should be covered in time and stored in the original packaging container.
Classified storage
Do not store LB2000 mixed with other different types of lubricants or chemicals to avoid chemical reactions that affect the performance of the lubricant.
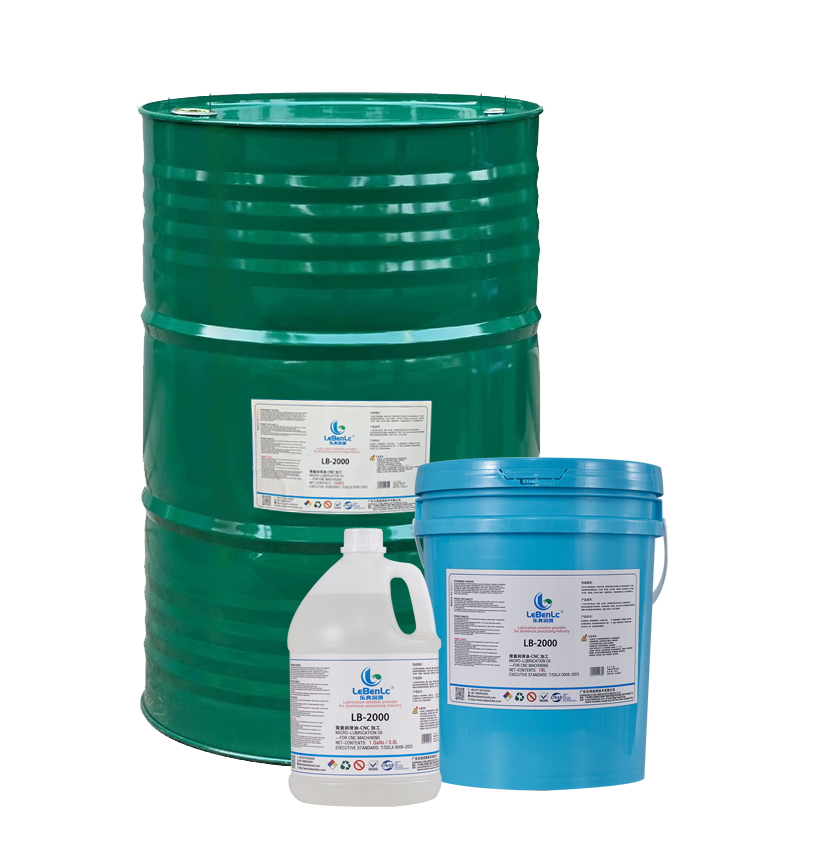